As summer approaches, Californians become concerned with wildfires and damage from burning. To relieve that anxiety, Kenneth Thomas provided an informative training on how to avoid burn marks on CNC projects.
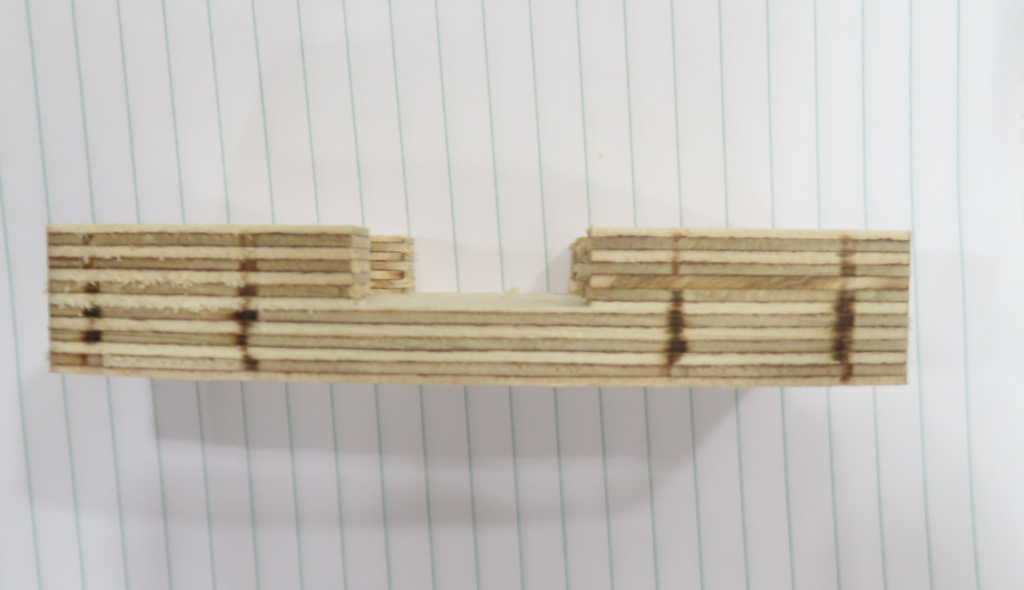
The lesson was held on June 3rd at the Rockler store in Ontario; there were 11 club members in attendance.
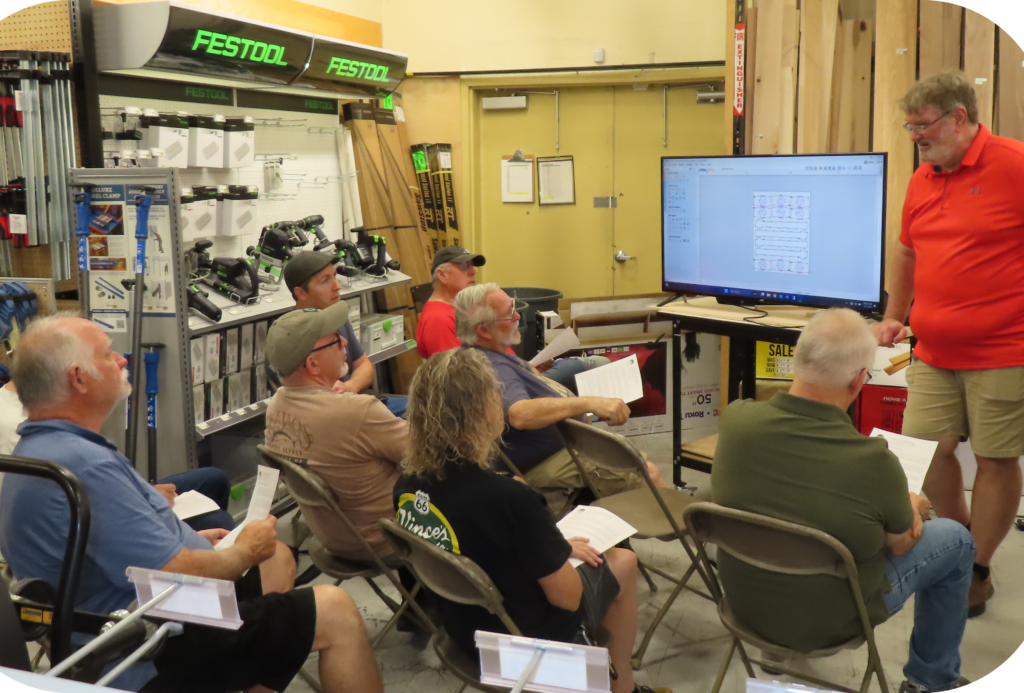
So, what causes burn marks? Some of the culprits include:
Speed: check your cutting speeds. Try adjusting the feed speed. Can your spindle turn fast enough? Is your machine strong enough to support the additional forces of faster speeds? Can the bit sustain the extra forces? Will it deflect, leaving the parts out of size? Will it break?
Entering the material: sometimes the method for entering the wood causes problems. Ramping might help, but sometimes the ramp cannot be achieved in a single pass. Vectric might travel back and forth while ramping down, which could lead to burning.
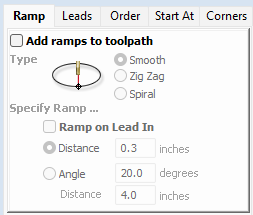
Experiment with the Ramp and Leads tabs in Vectric. Circular is better for cleanup than straight lead. If the lead-in is longer than the ramp, issues could arise.
Multiple passes: adding more passes might reduce tool heat but will add time to finish the job. Each pass could leave marks on the sides of the part. Try using a finishing cut to clean up tool marks and burn marks; 0.005″ is a good starting point. Vectric offers this feature in Tool Path as Last Pass.
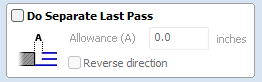
Material: check the hold-down: is the material sliding? Are there high spots?
Build up on the cutting tool: clean bits with a citrus-based cleaner (orange-aid, simple green) and a brass bristle brush.
Number of flutes: as the number of flutes increases, the travel should increase to clear the shavings. If the travel is too slow, the bit will rub against the part and cause burn marks.
Type of bit: straight bit vs up cut vs down cut vs compression bit. Compression bits push material up and down, which could lead to burning. Down cut bits require slower spindle speeds and feeds. Up cut bits leave the least amount of burning.
Carbide vs HSS: HSS doesn’t stay sharp as long. Carbide is expensive. There are cheap carbide bits available, but be cautious. The diameters are not always accurate, and sometimes they might be off center, leading to wobbles. Cheap bits often dull faster than quality bits.
Climb vs conventional milling: when cutting a slot, both are happening simultaneously.
Raffle
Thank you Rockler Ontario store for donating this month’s raffle prizes: discount cards, a shop apron, and a dust brush. Congratulations to this month’s winners: Rick Reimer, Matt Martel, Kris Fikel, and Kenneth Thomas.
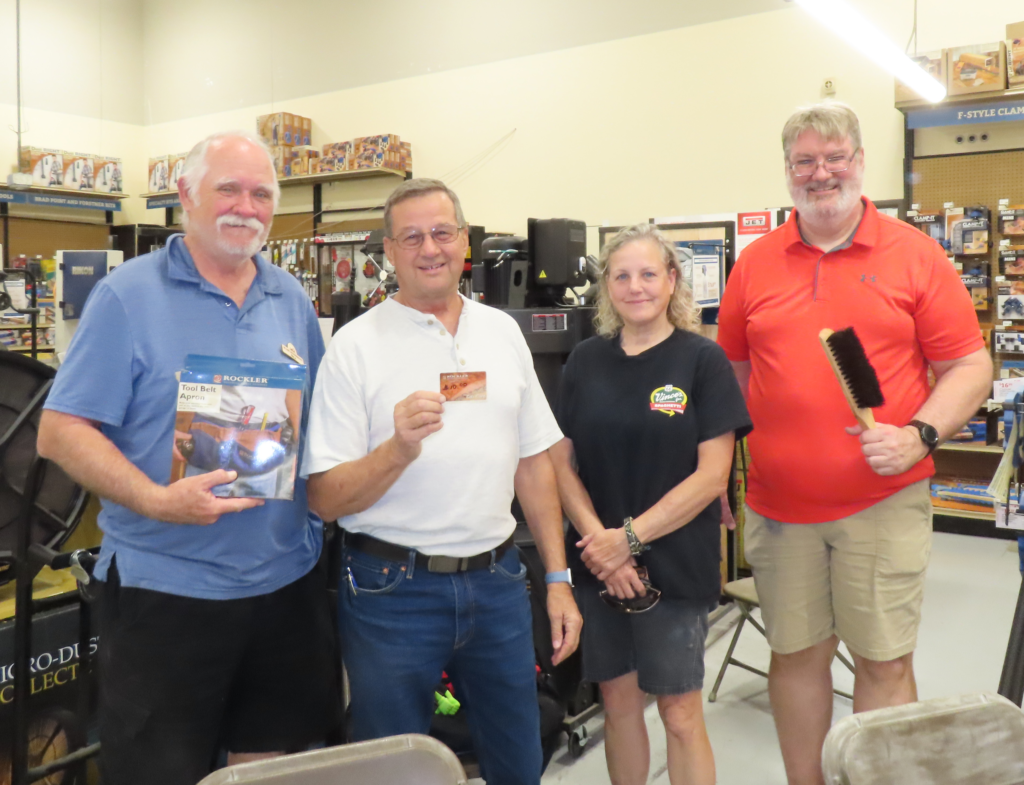
CNC Challenge
Last month’s training topic was text on text. This month’s competitors were Michael Miller, Keith Helberg, and Rick Reimer.
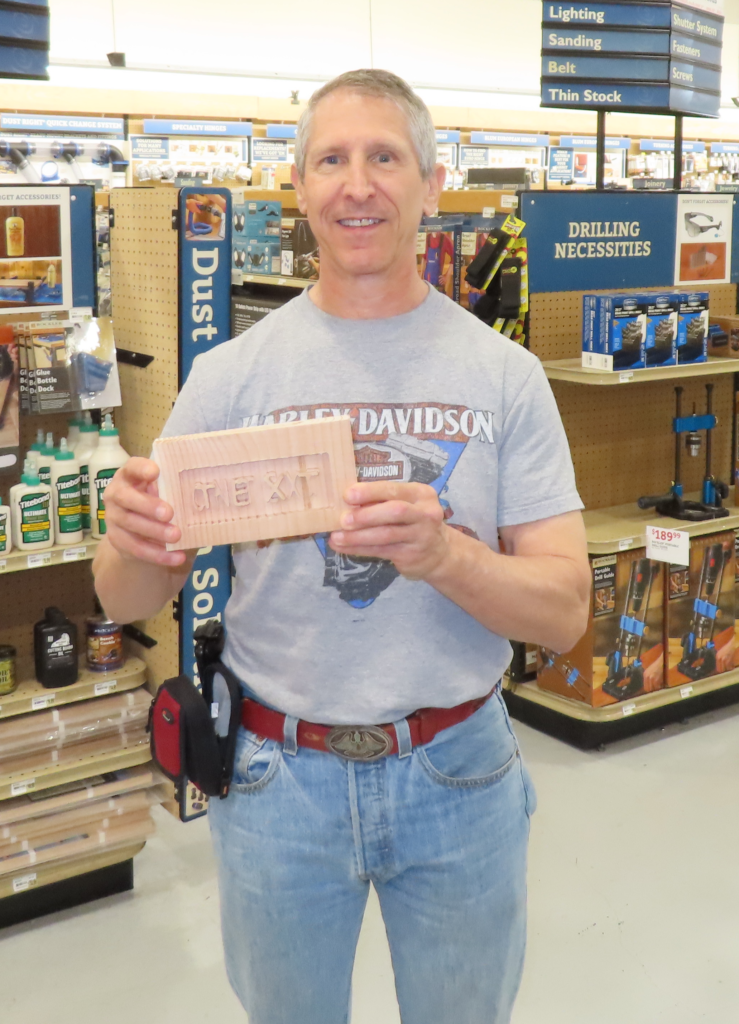

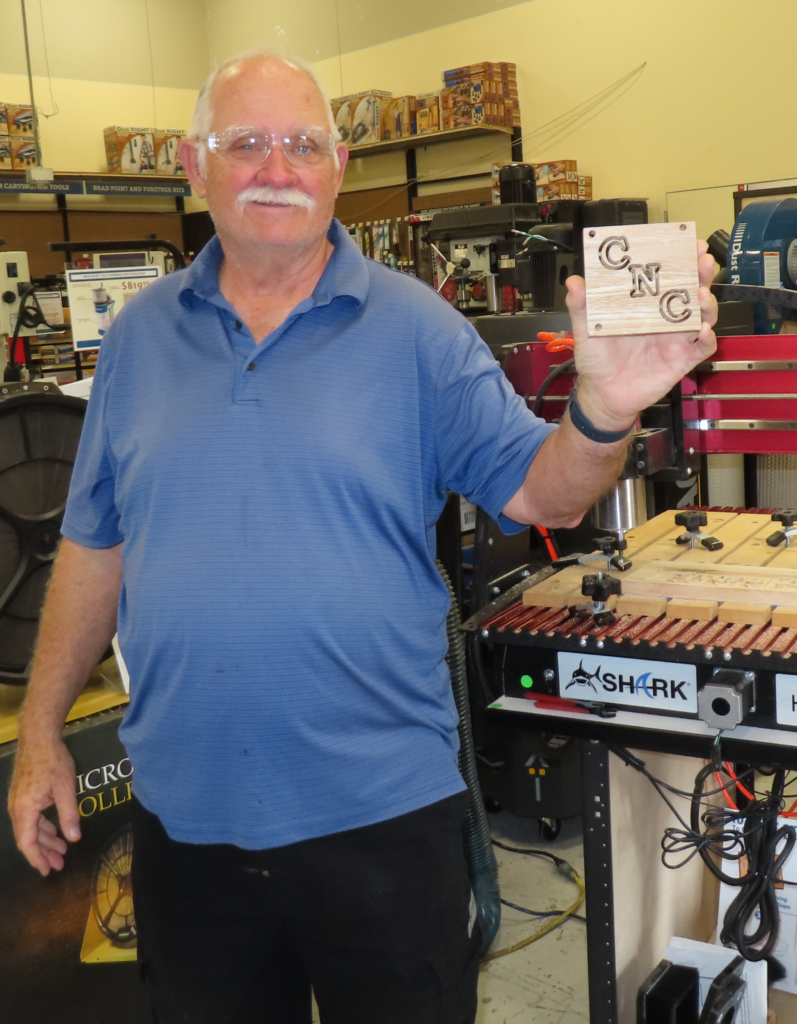
For next month’s competition, bring an example of a part exhibiting tool burns, and a similar part that does not have a burn, based on implementing one or more of the suggestions from today’s training.
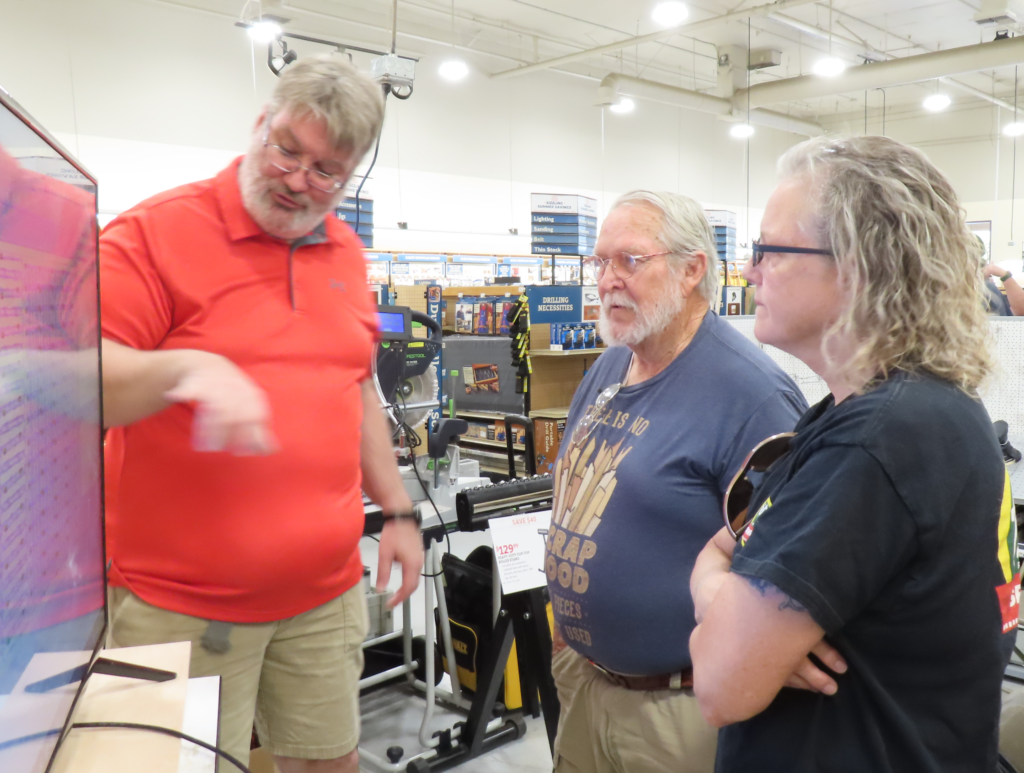
Reminder
Next’s month’s training has been moved out to July 8. Have a safe and enjoyable Fourth of July weekend.
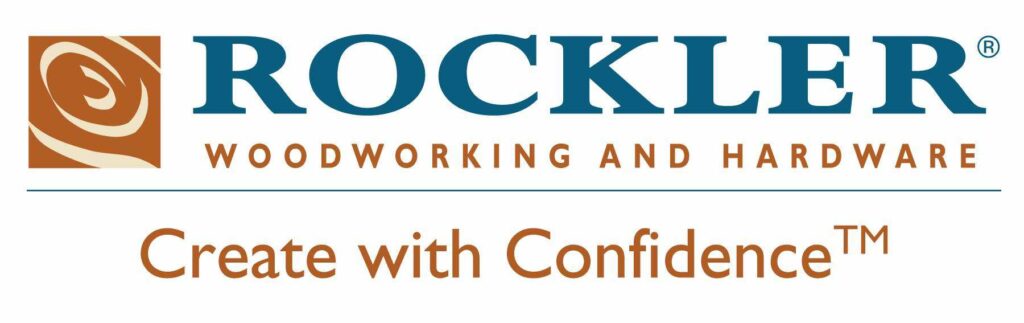